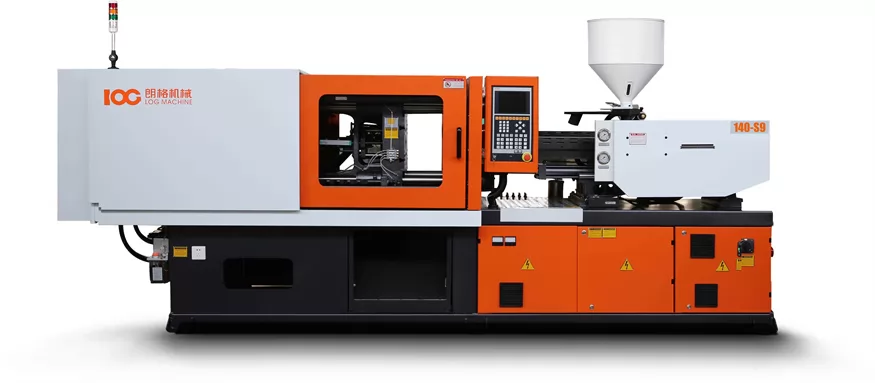
Hydraulic System
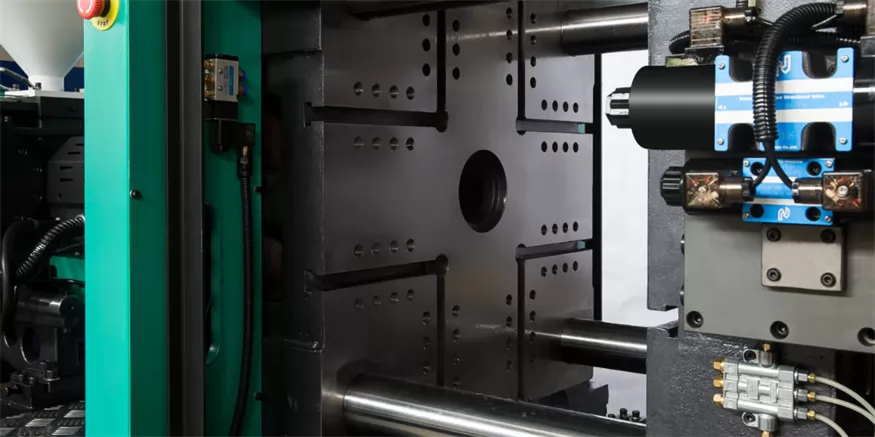
Electrical Parts
-
Safety
When checking the high-voltage parts in the machine, do not turn on the power of the machine unless it is necessary.
-
Wire connector inspection
The connector will not be tightened. The wires at the connector location may be damaged by heat or sparks. A bad connector will also affect signal transmission; due to vibration and electromagnetic release, the contactor connector is easier to move. Therefore, it is necessary to check the position of the cable connector and tighten it regularly.
-
Motor
General-purpose motors are air-cooled, and dust accumulation can cause heating problems, so they must be cleaned regularly every year. The motor overload cut-off device is usually installed in the circuit. The current limit of the protection device is adjustable. The electric power should be appropriately selected. Once the overload protection is activated, be sure to check whether there is phase loss, poor contact or high oil temperature after passing the position switch.
-
Heating tube and thermocouple
The heating tube should be fixed on the inspection to ensure effective heat transfer. The heat in a normal combustion cylinder is imperceptible. Pay attention to the working condition of the thermostat and judge whether it is normal from the heating tube.
-
Electromagnetic contactor
Contactors should be actively inspected and replaced in time due to frequent electric shock movement and rapid wear.
-
Computer control
The application of computer control technology in injection molding machines, parts and related auxiliary microcomputer electronic boards has very high requirements. Keep the ventilating fan of the control box working normally, use high-precision voltage stabilizing equipment to supply power, reduce the vibration of the control box to the outside, and check it regularly.
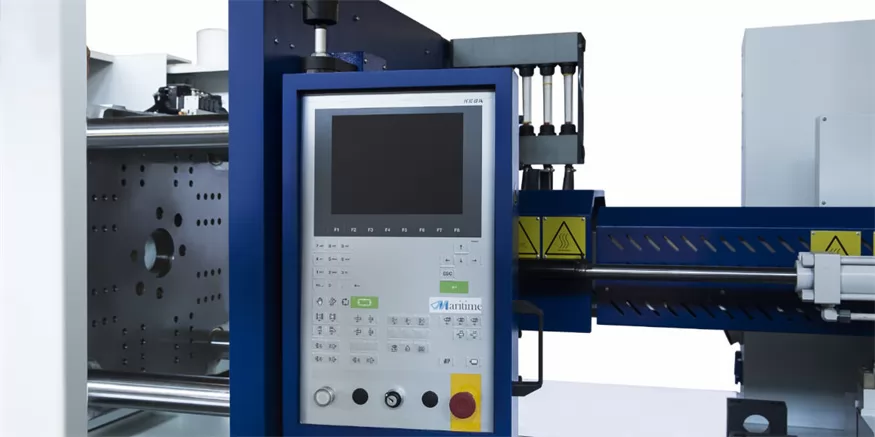
Mechanical Part
-
Template parallel
Familiar people should adjust the steps of the template in parallel, otherwise improper adjustment may damage the machine. Set the mold clamping stroke at the most suitable position to reduce the impact on the machine during mold clamping. Do not close the mold when the working pressure is insufficient or excessive. Do not run the fixture at too fast speed when adjusting the mold.
-
Mold thickness adjustment
Use the system to adjust the thickness of the mold regularly. The thickness of the module is adjusted from the thickest to the thinnest to ensure the stability and long-term production of the same mold. This check must be performed to avoid failure.
-
Clamping hinge
The long service life of the clamping hinge does not mean that the hinge does not require maintenance. Generally, each moving part should be properly lubricated (with lubricating oil or oil) to ensure that the service life of the hinge will not be shortened due to wear.
-
Bearing inspection
When the bearing is working, it makes an abnormal noise or the internal temperature rises, indicating that the bearing has been worn out. It should be checked or replaced in time, and grease should be added.
-
Injection system
Keep the guide rod on the injection platform lubricated and clean. Keep the surface of the injection platform clean and dry. Do not add materials other than plastics, paints and additives to the hopper. When using recycled plastics, be sure to put the magnetic hopper bracket into the hopper to prevent metal chips from entering the furnace.
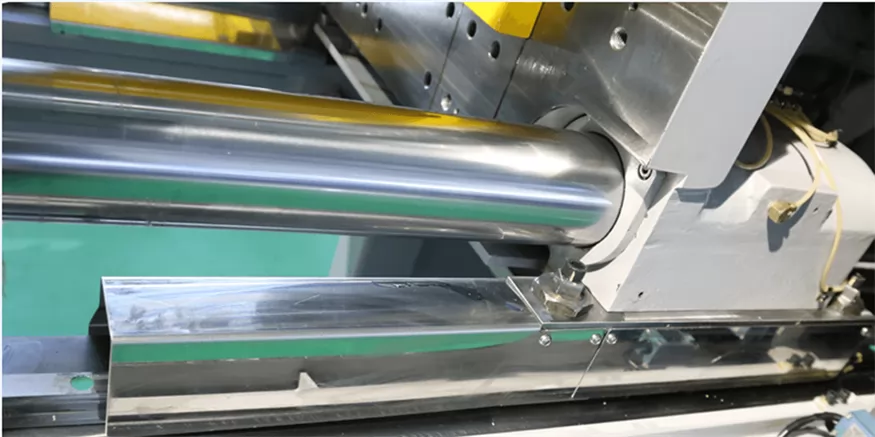
Conclusion
When the production line is under pressure and needs to deliver a large number of orders, even the completion of regular maintenance can help meet customer needs. In the long run, in addition to increasing costs, delayed maintenance will also start to bring costs to customers, including time and quality of production parts. Therefore, regular maintenance is very important to ensure that customers do not feel that there is a problem with the injection molding machine.
If you have more questions about the maintenance of the injection molding machine, you can contact us and we will give you the most professional answer.
We are a famous injection molding machine manufacturer from China. Our injection molding machines are sold worldwide. Also your trusted manufacturer