Servo injection molding machine is an important equipment for injection molding industry. In terms of its nature, components and uses, we will answer several frequently asked questions.
However, we will provide detailed and quality answers to your questions through this article. So relax, read through and get the enlightenment you want.
-
What is the guide to selecting a servo injection molding machine?
-
What are the disadvantages of servo injection molding machine?
-
What is the working principle of servo injection molding machine?
-
How can I maintain the quality of my servo injection molding machine?
-
How to improve the efficiency of servo injection molding machine
-
What technology is used in servo injection molding machines?
What is a servo injection molding machine?
In a servo injection molding machine, a servo motor is used instead of a normal AC motor. Servo motors can be used for all drives of the machine, such as pump motors and injection drives. Unlike a hydraulic servo injection molding machine that needs to run all the time, a servo motor will stop when the servo injection molding machine is not operating. Servo injection molding may mean servo valve control, servo drive or servo motor. In general, servo-driven injection molding machines are considered to be hydraulic machines with servo motors (regulated to variable speed) driving high quality, low noise pumps. For larger machines, more servo motor + pump units are deployed.
What is the guide to selecting a servo injection molding machine?
For more information:
How to choose the right injection molding machine
Servo injection molding machine selection guide
-
Determining the injection weight of a servo injection molding machine
There are too many servo injection molding machines in the market now. It is too simple to consider only servo injection molding machine, and the clamping force is not comprehensive. You need to combine the two to make a choice.
Injection weight is an important parameter of a servo injection molding machine, and it is the most useful and critical parameter for choosing a servo injection molding machine. Expressed in grams or ounces, this parameter is easy to understand, but it is also easy to misunderstand. The reason is simple. Once the plastic material is determined, the weight of the plastic part can be determined. Therefore, it is easy for them to choose a servo injection molding machine based on the injection weight. In fact, injection weight is defined as the maximum plastic injection weight that can be achieved by the injection unit when the screw makes the maximum injection stroke under the screw. Empty injection condition (not injected into the mold); this parameter reflects to some extent the processing capacity of the servo injection molding machine; it can be measured or calculated theoretically (theoretical and measured values may be different). The material used in the test is usually plain PS with a density of 1.05.
-
Steps to determine the injection weight
-
Calculate the product weight: W = product weight + weight of the gate system, where: W is the weight required for injection. In practice, there are two cases to be considered.
-
When the injection product is polystyrene (PS), the injection volume of the servo injection machine should be Wps; Wps = (1.3 ~ 1.1) × W (product weight + total weight of gate system), when the product requirement is high, the coefficient in the above equation should take a large value, and vice versa can take a small value.
-
When the product is an imitation of other plastic (named X plastic), first calculate the theoretical injection volume of the plastic should be Wx; Wx = (1.3 ~ 1.1) × (product weight + total weight of the gate system); then convert to the actual weight of PS material Wps according to the density of plastic (X), the conversion formula is: Wps = Wx × 1.05 / Vx
-
According to the calculation result of Wps and LOG manual, choose the suitable servo injection molding machine.
Note: The relationship between injection weight and injection volume
-
Injection weight is not only the injection volume multiplied by the density of PS. The injection weight is measured and the injection volume is the theoretical value. Since the plastic will flow into the gap between the barrel and the screw when injecting, and the check ring needs to move backward to reach the closing position, the injection volume is doubled because the density of PS is greater than the injection weight.
-
For less demanding products, such as toy dolls: the total weight should be 85% of the injection weight; in highly demanding injection molding; such as crystal products, 75%.
-
Do not use a servo injection molding machine with too much injection weight
The total weight of plastic and runner plastic should be between 35% and 85% of the injection weight. The lower limit is due to three considerations: the bending of the sheet; the residence time of the plastic in the barrel and the power consumption per kilogram of the injected part. Small injection molded parts using small molds can cause excessive bending of the platen, resulting in warpage (which affects product quality) and even platen cracking. Injection molding small plastic parts with oversized servo injection molding machine. If the residence time of molten material is too long, it may cause the molten plastic in the barrel of the machine to decompose.
-
Injection speed
For ultra-thin-walled products, the use of high-fluidity materials to make the molten plastic flow at ultra-high speed, to ensure that the molten material contact the mold wall after cooling and solidifying the formation of the surface layer thickness l for the thinner the better, is to try to delay the generation of solidification skin time. So it involves the problem of injection speed. According to experience, the injection speed can be 1 to 1.5 times of the flow length ratio.
-
-
Calculation of clamping force of servo injection molding machine
There are two important factors to calculate the clamping force: 1. projection area; 2. cavity pressure.
-
The projected area (S) is the maximum area seen by the line of sight from the mold opening and closing.
-
Cavity pressure determination (P)
-
The cavity pressure is influenced by the following factors
-
Number and position of doors
-
Door size
-
Thickness of the product
-
Viscosity characteristics of the material used
-
Injection speed
-
Grouping of thermoplastic flow properties
Group 1 PS PE PP
Group 2 PA6 PBT PET
Group 3 PU Soft PVC
Group 4 ABS as POM
Group 5 PMMA PC/ABS PC/PBT
Group 6 PC PEEK Rigid UPVC
-
Viscosity Grades
Each of the above groups of plastics has a viscosity (flowability) grade. The relative viscosity grades for each group of plastics are as follows
Group multiplication constant (K)
Group I × 1.0
Group II × 1.3 to 1.35
The third group × 1.35 to 1.45
Group IV × 1.45 to 1.55
Fifth group ×1.55~1.70
Sixth group×1.70~1.90
-
Cavity pressure is determined by the wall thickness, the ratio of flow rate to wall thickness
P = P0 - K (multiplication constant)
-
Clamping force (F) determination
F=P-S=P0-K-S
-
-
Power and torque
First of all, choose the servo system with higher power and torque, which will directly affect the overload capacity during the high pressure action. The ultimate performance of the machine can be tested physically, for example, by using the highest pressure for a long time load and testing the machine state after several cycles.
At present, servo motor magnets have M, S, H, SH grade, SH is the highest grade, the magnetic flux is the largest (that is, the number of magnetic lines per unit area), high torque output more advantages of good overload capacity; avoid using cheap servo system, because the servo system overload for a long time, the servo motor is prone to demagnetization, so that the power of the machine appears to decline.
-
Motor and oil pump
Pay attention to the motor and oil pump coupling, whether to use a reliable coupling and bracket structure, because the servo motor in the operation process will be frequent acceleration, deceleration, braking, reversal, and completed in a few tens of milliseconds, which will affect the drive process of axial concentricity and buffering, from then on affect the motor bearings, oil pump life.
-
Displacement and rotational speed
Pay attention to the oil pump displacement, rotational speed and other data affecting the machine operating efficiency, the larger the oil pump displacement at the same speed, the higher the machine operating efficiency, the highest flow output requirements and the relationship between rotational speed should be considered when selecting the oil pump displacement, in order to ensure the highest flow output requirements, it is recommended that the rotational speed is designed within a reasonable safety range to ensure the reliability and service life of the servo drive system, low speed design also brings response speed Faster, but this will increase the cost of the machine, involving the price positioning of the machine.
What is the difference between servo injection molding machine and normal servo injection molding machine?
The difference between the two is the motor.
Ordinary injection molding machine: it keeps operating, even if the machine action stops, the motor keeps turning.
Servo injection molding machine: Each different action will use the corresponding power to provide power, as if the machine is not moving, the servo motor will stop completely. Save a lot of electricity
What are the elements of servo injection molding machine?
Servo energy saving system will be the six elements of servo injection molding machine power system.
-
Servo motor
-
Encoder
-
Gear pump
-
Servo drive
-
Pressure sensor
-
Drive control module
Its specific working process and key technologies can be summarized as follows:
-
The servo driver accepts the pressure (P) and flow (Q) commands issued by the servo injection molding machine controller and converts them into speed commands to the servo motor. The servo motor drives the gear pump to rotate, and the gear pump outputs the pressure flow rate as instructed, while the pressure sensor collects the system pressure information and feeds it to the servo driver, and the servo motor feeds the speed information to the servo driver. Subsequently, the servo driver feeds the actual pressure and flow information to the servo injection molding machine controller through conversion. By comparing the actual flow rate and pressure with the commanded flow rate and pressure, the servo injection molding machine controller adjusts the commanded flow rate and pressure in a timely manner, thus realizing closed-loop control.
-
The response speed of the servo system can reach 0.03ms, which is much faster than the response speed of 0.3ms of the variable pump, thus significantly improving the control accuracy.
-
Another key design point of this system is the selection of a suitable servo system for the servo injection molding machine. Here, this servo injection molding machine changes the design method of servo injection molding machine power configuration: the power configuration of the servo injection molding machine is selected directly from the product requirements, and the pressure, flow rate and time requirements are listed for each step of injection molding, so that the actual power required for each step can be calculated, and then the power for the whole cycle can be calculated to determine the selected servo power configuration. The advantage of this is that the power requirements are strengthened and clarified from the details of each step, so that they not only meet the production requirements of the products, but also happen to be able to fully meet the production requirements, thus controlling the energy waste from the source and achieving energy saving effect.
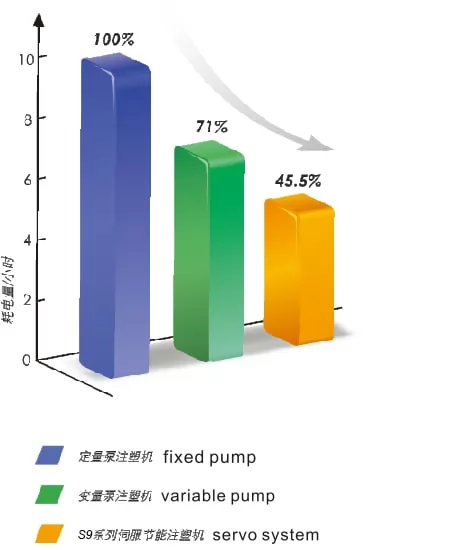
1. Realize real-time monitoring of various signals such as actual pressure, flow rate, drive output current, load rate, etc. through bus high-speed communication.
2. Medium-sized injectors with double pumps or multi-pump merging mode use special servo control technology to achieve perfect synchronous control of servo and oil pumps and perfect merging of multiple oil pumps
3. from rich field service experience, convenient and fast parameter debugging, can meet the production needs of different users.
4. realizing multi-pump merging, which can realize intelligent control of master/slave pumps
5. built-in DC reactor, high reliability and low failure rate.
6. with a variety of protection methods such as phase loss, short circuit, overheating detection, to ensure the safe and stable operation of the servo injection molding machine.
7. Compact structure, saving the internal space of servo injection molding machine.
8. Servo injection molding machine uses servo motors for opening and closing the mold, ejecting and demolding, injecting and storing raw materials, etc.
9. Fast operation speed and high precision greatly improve or enhance the production environment and production efficiency.
10. Response speed can reach 0.03ms, much higher than 0.3ms of variable pump, thus significantly improving control accuracy.
What are the disadvantages of servo injection molding machine?
General ordinary servo-driven servo injection molding machine is to add a servo drive machine on top of the servo injection molding machine. Disadvantages are as follows.
-
Tthe degree of vulnerability to damage. After the addition of the servo drive system, the servo drive system will have the possibility of failure and damage, which is more than the servo injection molding machine without the servo drive system, there is an additional point of failure.
-
Servo injection molding machine of the entire work process of the oil pump motor power loss is serious, the power utilization rate of only 30% - 70%, therefore, its power saving space is relatively large.
Log has made improvements on this basis, making the LOG-S8 series servo injection molding machine with the following advantages.
-
Energy saving
-
High precision
-
Fast response
-
Longer life
-
Economical
What is the difference between a normal servo injection molding machine and a fully electric servo injection molding machine?
A hybrid servo injection molding machine will have some servo-assisted drives as well as a hydraulic system.
The all-electric will use a full servo drive with no hydraulics. The servo motor used in the all-electric servo injection molding machine can open and close the mold, eject the mold, inject the raw material into the storage, etc. The operation speed is fast and high precision, which greatly improves or increases the production environment and production efficiency.
Read more:
Electric vs. hydraulic injection molding machine
8 reasons to buy all-electric injection molding machine
What is the working principle of servo injection molding machine?
Servo injection molding machine has the ability to mold plastic products with complex appearance, precise dimensions or dense texture with metal inserts in one go. It is a process of injecting plastic in a molten state (i.e. viscous flow state) into a closed mold cavity with the help of the thrust of a screw (or plunger) and obtaining products after curing and shaping. It is widely used in national defense, electromechanics, automobile, transportation, building materials, packaging, agriculture, culture, education and health and people's daily life in various fields.
Servo injection molding machine is based on the required pressure and speed to control the speed of the motor, the speed is very low when holding pressure, when cooling, only the fan will turn, so the longer the two actions the more power saving, but the melt glue when the power consumption is larger, and sometimes more than the power consumption of the quantitative pump.
How can I keep the quality of servo injection molding machine?
Since servo injection molding machine is a very important equipment, even the cost effective domestic servo injection molding machine, the price and maintenance cost is not a small amount. Therefore, there are several very important considerations for the maintenance of servo injection molding machines.
-
The maintenance, repair and servicing of the machine must be carried out by experts who are sufficiently qualified and experienced in the field of servo injection moulding machines. They should be familiar with industrial life and safety standards, and should be familiar with the structure and function of the necessary machine safety equipment.
-
All maintenance work must be carried out with the main power switch of the servo injection molding machine set to "0". If necessary, lock it with a padlock.
-
It is the responsibility of the employer to make the operator aware of the structure and function of the safety facilities and to take personal health and safety seriously.
-
Any work that would damage the machine's safety features should be stopped.
-
The employer must ensure that the operator is an experienced and qualified operator.
-
Under no circumstances should safety features be disconnected from the machine or fail to function properly. If the safety device needs to be removed for machine maintenance, safety must be ensured. After the repair work is completed, install the safety device as it is and check the effectiveness.
-
No unauthorized alteration of safety facilities is allowed!
In addition to the inspection before and after the daily work, the servo injection molding machine should be inspected regularly. This is very important for the normal use and smooth operation of the servo injection molding machine, and can save a lot of maintenance costs.
Monthly inspection
-
Check the quality of hydraulic oil and find impurities in the oil. If the oil is insufficient or contains water, it must be dealt with promptly. Replenish the insufficient hydraulic oil.
-
Check whether the circuit is loose at each point.
-
Check the ventilation filter on the electric control box, remove dirt, and remove and clean if necessary.
-
Clean the hydraulic oil filter.
-
Clean and treat each movable surface (such as the sliding guiding surface of the tie rod and injection seat), and then reapply new lubricating oil.
Annual inspection
-
Check the quality of the hydraulic oil. Generally the hydraulic oil used in servo injection molding machine needs to be replaced with new oil once in 1-1.5 years: when using new equipment, the hydraulic oil should be drained from the hydraulic system of the servo injection molding machine after 3 months of use, and control the various controls in the hydraulic system. Valve, pipeline, oil tank cleaning once (because the iron powder and unclean debris worn in the pipeline is mixed into the oil in the initial stage of the new equipment), filter the hydraulic oil (use 150 mesh filter), and add the mailbox.
-
Correct the temperature difference error between the thermocouple pyrometer display and the actual temperature measurement point of the pyrometer; remove the dirt on the thermocouple contact points and correct the correct working temperature measurement position of the thermocouple.
-
Check the solidity of all junction points in the control box, check whether the rubber insulation layer of the circuit is aging to prevent leakage, and replace the electric line if necessary.
-
Check the mechanical drive reduction system, such as the cleaning of the bearings, check the wear and tear, and replace the bearings if necessary. Check the wear of the gear teeth and the quality of the lubricant in the gearbox. Make a record.
-
Check the wear of the screw and barrel, refurbish minor wear and scratches, repair if the wear is serious, make a record and propose a replacement plan.
-
All drive motors, hydraulic pumps and motors should be disassembled and inspected to check the wear of bearings and pump bodies. After cleaning, add lubricant (grease), record the wear parts, and propose repair or replacement plan.
-
For some sealing rings. Check and replace wearing parts when necessary.
Detailed reading.
Injection molding machine maintenance: what you need to know
China injection molding machine maintenance guide
How to improve the efficiency of servo injection molding machine
By checking and ensuring that the machine is well cleaned and observed when you need to clean and save the equipment.
As a result, you can also improve the productivity of your equipment by eliminating or eliminating and inheriting components from the instrument.
Replace components only when necessary, as this is important to increase the productivity of the equipment.
What is the cost of a servo injection molding machine?
The price of a servo injection molding machine varies very much depending on the brand, depending on the model and specifications of each manufacturer. But the operating cost in the production process of injection molding industry is a very important part. Servo injection molding machine can generally save 40-60% of electrical energy, significantly reducing energy costs.
Read more: What is the price of injection molding grade
What technology is used in Log production servo injection molding machine?
-
Mold clamping parts
-
The injection parts adopt double cylinder balance design, higher injection pressure, simple and stable structure. Shorter design space. Low failure rate.
-
Increased injection displacement cylinder, large models adopt double injection displacement cylinder structure, which effectively prevents the injection nozzle from leaking due to machine vibration and other reasons when the machine is running at high speed.
-
Graphite bushings are used for injection guide bushings to improve the wear resistance of bushings, reduce the frequency of adding lubrication to bushings and effectively improve the cleanliness of injection parts.
-
The injection cylinder and injection cylinder adopt low friction seal to improve the injection response rate and provide injection stability under complicated process.
-
The overall design of bridge type injection table base is suitable for plasticized parts with different aspect ratios.
-
-
Injection parts
-
The front connecting rod adopts a one-piece structure, which improves the rigidity of the connecting rod and ensures the consistency of the processing size of the connecting rod. It can reduce the fit clearance of the pin and cylinder liner. Ensure the precision of the connecting rod mechanism and improve the service life of the connecting rod mechanism.
-
The locking head plate adopts box structure design, the thickness of the template and the internal strong tendons are thickened to improve the rigidity of the head plate and more effectively reduce the bending deformation of the tie rod when it is under pressure.
-
The unique design of tail plate flange in CU model, when the tail plate is deformed by the force, through the tail plate flange and tie bar support, the reverse torque with the deformation of the tail plate is generated, so as to reduce the deformation of the tail plate.
-
Adopt the gears to adjust the mold structure with high repetition accuracy and large adjusting force.
-
-
Low noise
The hydraulic control structure is reasonably designed and highly integrated, and the unique noise reduction treatment makes the machine run smoothly and quietly, making the working environment more comfortable.
-
Low oil consumption
The reduction of oil temperature greatly extends the service life of the seals, and the oil cleaning system can quickly and effectively filter the oil dirt to ensure the service life of the hydraulic parts.
-
Control system
-
Humanized computer operation interface is easy to operate, the operation box can be rotated design, easy to operate.
-
Optimized electrical design, using a well-known brand servo injection molding machine special computer, fast response time, reliable control.
-
The information in the production process of the equipment is completely saved, and the different display methods such as data list and graphics are fully in line with the actual application needs.
-
-
Servo energy saving system
-
Servo injection molding machine through the bus with high-speed communication to achieve real-time monitoring of the actual pressure, flow, drive output current, load rate and many other signals.
-
Servo injection molding machine of large and medium-sized injectors using double pumps or multi-pump merging mode, the servo uses special control technology to achieve perfect synchronization of servo oil pump control, to achieve the perfect effect of multiple oil pumps merging.
-
Read more: China's injection molding machine development trend
If you are looking for the right servo injection molding machine, welcome to check out LOG Machine's servo injection molding machine products!